How easy it would be to cut through metal like a knife through butter. Yeah, but you know that’s possible, right? With a plasma cutter, you can cut through almost all types of metals you work with. As an industry or a DIY routine at home, consider the plasma cutter as your reliable tool. Join me; let’s figure out how to use a plasma cutter and understand the essentials of operating it.
Knowing how to use this tool well can revolutionize your approach to fabrication and DIY projects that involve metals, making your work a whole lot easier. Let’s embark on this journey together, starting with how to set up a plasma cutter to make the most out of it for efficiency.
How to Set Up a Plasma Cutter for Use
Plasma cutters have become a really essential tool for many industries. With advancements in technology, they are now more accessible to DIY enthusiasts as well, especially those in the metallic industry.
A good brand for plasma cutters is VEVOR. They have lots of quality tools and machines for industrial and home purposes. Plasma cutter devices employ an electric arc and compressed gas to cut through different metals precisely. Properly configuring a plasma cutter is vital for safety and optimal functionality. Let us walk through some of the setup processes you need to follow to get your plasma cutter ready for use.
Whether you are a professional welder or a hobbyist working with metals, having a proper plasma cutter setup is crucial to ensure safe and efficient operation. It would save you a lot of time and effort if you do this properly.
Check and ensure the safety of the equipment before using
Before using a plasma cutter, make sure it’s safe. You can check for any damages that could be a safety hazard or affect its performance. Now examine the power cord, too, and inspect the torch and connections to ensure they’re secure. Finally, verify the gas supply for leaks or loose connections. Take a moment to understand the safety features, including the emergency stop button, and wear the necessary protective gear.
Make sure the workpiece and the plasma cutter are grounded
Grounding serves two crucial purposes. Firstly, it safeguards the operator from electrical shock and potential harm by directing stray currents safely into the ground. This will help minimize the risk of accidents. Secondly, grounding the plasma cutter will contribute significantly to improving cutting performance by stabilizing the plasma arc, ensuring consistent and reliable cutting quality.
Follow manufacturer specifications and adjust the air pressure and flow rate
Make sure you stick to these rules to avoid any mishaps, keep your equipment in good shape, and make it run smoothly. It’s super important to tweak the air pressure and flow rate as per the specs for the best outcome. Straying from these guidelines not only affects performance but also puts you at risk. Don’t forget to check the manufacturer’s instructions and set the air pressure and flow rate just right for top-notch operation and safety.
Install the appropriate consumables for the material and thickness being cut
Now, what is the plasma cutter used for? For cutting through metals, right? So, when preparing the plasma cutter, make sure to install the right consumables based on the material and thickness you’re cutting. This ensures clean and accurate cuts. Various materials and thickness levels demand specific consumables like electrodes and nozzles. Incorrect choices can lead to subpar cutting, shorter consumable lifespan, and higher operating expenses. Refer to the manufacturer’s guidelines or seek expert advice to identify the appropriate consumables for your specific cutting task.
Also, don’t forget to make sure you have sufficient space for both the machine and the metal you plan to cut with your plasma cutter. Ensure enough room for maneuvering the metal, positioning it accurately, and smoothly navigating the cutting process. Having sufficient space is crucial to prevent accidents or damage to the machine and the material being cut.
How to Use a Plasma Cutter
Now, what is the plasma cutter used for? For cutting through different metals with precision and ease, using a plasma cutter can be really helpful and save you a lot of time, especially when you know how to use it. This is why it’s a good idea to learn how to go about it properly. And let’s not forget the fact that you have to use the best tools. Not every plasma cutter is efficient or even comes with a manufacturer manual for safe handling.
VEVOR has some of the best products when it comes to plasma cutting. Offering a wide range of plasma-cutting machines to cater to different needs and budgets. From compact and portable models for small-scale projects to heavy-duty machines for industrial applications. Let’s go over how to use a plasma cutter effectively.
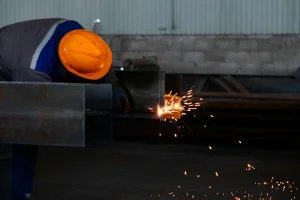
1. Turn on the plasma cutter and adjust settings
- Set cutting mode
To get started with a plasma cutter, first, power up the machine by locating and flipping the switch to the “on” position, usually found on the front or side. Once powered on, adjust the settings using the control panel. Focus on crucial parameters, such as cutting mode, which includes options like straight line cutting, bevel cutting, and gouging. Choose the appropriate mode for your project to determine the plasma stream’s angle and direction. With the cutting mode set, you’re all set to use the plasma cutter for accurate cuts on different materials.
- Select material type and thickness
After firing up the plasma cutter, be sure to configure it according to the material at hand – be it steel, aluminum, or stainless steel. Each material requires specific settings for optimal cutting outcomes. Don’t forget to factor in the material thickness, as it significantly impacts the precise and efficient cutting settings. Picking the correct material type and thickness guarantees excellent results from the plasma cutter.
2. Ignite the arc
- Take the torch close to the workpiece
Now, how do you use a plasma cutter? By using the arc. To kick-start a plasma cutter’s arc, gently approach the torch to the workpiece. This guarantees the initiation of the plasma arc, initiating the cutting process. The torch’s proximity to the workpiece is critical for triggering the required plasma reaction. Proper positioning enables the plasma’s intense heat to melt and vaporize the metal, facilitating accurate and efficient cutting. Bringing the torch near the workpiece allows you to leverage the plasma cutter’s power and attain the desired outcomes.
- Press the trigger to initiate the arc
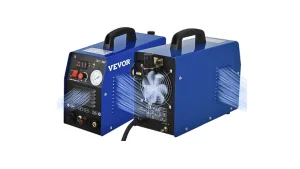
To start plasma cutting, just press the trigger to ignite the arc. This triggers a sequence in the cutter, where the high-frequency electric current flows through the torch into the electrode. The electrode, surrounded by a gas mix of nitrogen, oxygen, and argon, conducts the current. As the current passes through, it heats the gas, turning it into plasma. This rapid plasma is then expelled from the torch, allowing precise and effortless cutting across various materials.
3. Cutting techniques
- Maintain a steady control
For optimal results when using a plasma cutter, maintain a steady hand and control your cutting speed. Ensure a consistent distance from the material to prevent uneven cuts or tool damage. Maintain a firm grip to minimize unnecessary movements. Practice correct hand and body positioning for precise and efficient cuts.
- Follow the designated cutting path
When operating a plasma cutter, stick to the assigned cutting path. This method guarantees accurate and precise results in shaping or patterning. Adhering to the designated path not only prevents mistakes but also enhances safety by preventing the cutter from straying and causing harm to materials or oneself. It’s a key step to ensure the final product aligns with the necessary specifications. Hence, it’s vital to be attentive and scrupulously stick to the assigned cutting path when utilizing a plasma cutter.
- Adjust torch level to maintain a perfect cutting distance
When using a plasma cutter, ensure optimal results by employing correct cutting techniques. Adjust the torch level to maintain an ideal cutting distance – the space between the plasma torch and the material. Avoid inefficiency by keeping the torch neither too far nor too close; the former may impede the cutting process, while the latter can cause excessive heat, potentially damaging the material. By fine-tuning the torch level for the perfect cutting distance, users can achieve clean, precise, and efficient cuts with their plasma cutters.
- Shut down the plasma cutter after completing the cut
Turn off the plasma cutter once you finish cutting. This saves energy and enhances workspace safety by minimizing the risk of accidental fires or injuries from hot metal. It also extends the equipment’s lifespan by preventing unnecessary wear and tear. So if you want to use your plasma cutter for a really long time, then I suggest you turn it off when you are not using it.
Safety Precautions on Using a Plasma Cutter
When operating a plasma cutter or even a welding cart, like any powerful tool, it’s essential to observe safety measures to prevent accidents and prioritize the operator’s well-being. Before you have your plasma cutter setup, here are a few safety precautions you should keep in mind.
1. Popular protective equipment
- Fully covered safety glasses: Wear fully covered safety glasses for complete eye protection, to shield your eyes from flying sparks, debris, and harmful UV rays produced by the plasma arc.
- Heat and flame-resistant clothing: Always put on heat and flame-resistant attire for protection. This will help shield you against extreme heat and sparks, handling temperatures up to 2000 degrees Fahrenheit.
- Welding gloves: Welding gloves protect your hands and wrists from the searing heat and sparks produced during cutting.
- Respirator to enhance healthy breathing: Always wear a respirator designed to protect your lungs. Choose a respirator with a high-efficiency particulate air HEPA filter to effectively filter out hazardous particles, maintaining clean and safe air.
2. Work in a ventilated environment
Make sure to operate your plasma cutter in a space with good ventilation. You can ensure proper ventilation by using exhaust fans or opening windows and doors for fresh air circulation.
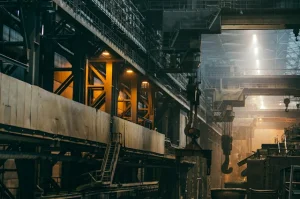
3. Don’t keep any flammable materials
When operating a plasma cutter, make sure no flammable materials are close by. The high heat produced by the machine can ignite nearby flammables, creating a fire risk and potential accidents or injuries.
4. Turn off the power when adjusting or changing the equipment
Always switch off the power before making adjustments or changing equipment with a plasma cutter. Turning off the power minimizes the risk of electrical shock or equipment damage.
5. Familiarize with first aid equipment and situations
It’s important to be familiar with the necessary first aid gear and potential situations that may arise when using a plasma cutter. Since plasma cutters produce intense heat, caution is key to avoiding severe burns. You can also use a fume smoke extractor to help filter the air while you work.
Troubleshooting Tips on How to Use a Plasma Cutter
1. Get to know the common cutting issues
When using a plasma cutter, it’s very important to know some common cutting issues., so you can address them easily when they come up.
- Dross or slag on the cut edge often results from factors like excessive cutting speed or insufficient amperage.
- Uneven or jagged cuts may stem from a worn-out or incorrect cutting tip.
- If the plasma cutter isn’t fully cutting through the material, check for low air pressure or a worn-out electrode.
2. Change settings or techniques to address problems
Consider slowing down the cutting speed or increasing the amperage to solve the Dross or slag on the cut edge. Swapping it out for a material-specific new tip is recommended. if you are experiencing uneven or jagged cuts. Adjusting air pressure or replacing the electrode can resolve this issue when the plasma cutter isn’t fully cutting through the material.
3. Can you weld with a plasma cutter?
Most people ask, can you weld with a plasma cutter? The answer is yes, it is possible. Although a plasma cutter is mainly designed for metal cutting, it can also serve as a multi-functional welder.
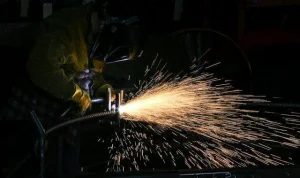
Widely utilized in industries demanding top-notch weldings, such as aerospace and automotive manufacturing, it’s important to acknowledge that plasma welding involves specialized equipment and expertise. So you should make sure you know what you are doing before you go ahead.
4. Perform regular maintenance checks
To maintain your plasma cutter’s optimal condition, regularly inspect and clean the torch and consumables. Remove accumulated debris to prevent hindrance to the plasma arc, ensuring consistent cut quality. Replace worn-out consumables like electrodes and nozzles for efficient cutting. Check and clean air and gas filters, as well as the cooling system, to prevent clogs or overheating. These routine checks enhance the reliability and lifespan of your plasma cutter.
Conclusion
Wrapping up, remember to choose a ventilated area, secure your material, tweak the settings for thickness and type of material, and fire it up. Keep a steady hand along the marked line, steer clear of abrupt moves, and voila – a clean cut with your plasma cutter!
Now you are covered on how to use plasma cutter. Setting up and operating a plasma cutter should be easy now. However, you need to stay safe when using a plasma cutter! That powerful plasma beam can cause burns or injuries if you’re not careful. Suit up in gloves, goggles, and a plasma-cutting-ready welding helmet. Remember to ensure proper ventilation. You can use a solder fume smoke extractor or exhaust fans. Practice and get comfortable with the machine settings for safe and precise cuts.
Remember, regular practice builds confidence and proficiency, giving you the experience you need to minimize the risk of accidents. Mastering plasma cutter skills can be achieved while prioritizing safety.
Our recommended choice is VEVOR products if you are looking to buy a plasma cutter for your metal projects at home or for industrial use. You can also get other equipment like the respirator and safety glasses that would make your metal cutting experience go smoothly and safely. VEVOR has all you need and you can have peace of mind knowing that you are investing in reliable and durable equipment that will enhance your metal-cutting abilities.
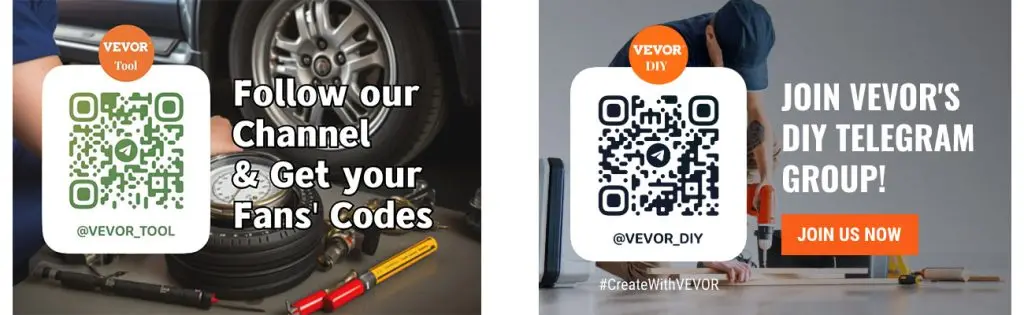