Introduction
Are you facing difficulty in choosing the air compressor for plasma cutter? The choice can be super confusing, with so many options to consider. The absence of the right compressor can prevent you from plasma cutting efficiency. Generally, noise, size and power are the top issues. You want a compressor that you can afford and meets your cutting requirements. Plasma cutter requirements comprehension is essential. Don’t you know the pain of trial and error? Fear not! By following the tips that are few in number, you can get the ideal air compressor for your work. We will start with the fundamentals and then help you with your plasma cutting to make it easier and more productive.
Table of contents
Part 1: Why Do You Need an Air Compressor for Plasma Cutter?
Having an air compressor for plasma cutter is compulsory, which is indispensable for perfect performance of the device. Without the gas, your plasma cutter simply will not function. Here’s why:
- Air Pressure for Cutting: These compressed air powered plasma cutters are designed to use the plasma arc to sever different materials. The compressor supplies pressured air that the cutter transmits to the plasma arc.
- Cooling and Shielding: Compressed air is not only serving as the plasma arc source, but also cooling the cutting torch. Jet air cleans away the molten metal and garbage at high speed, thus ensuring the cleanness of the torch and neat tracks. Likewise, the bubble of air reduces the interference from the atmosphere.
- Consistency and Precision: The plasma-arc stability and precision are based on an uninterrupted compressed air supply. The change in air pressure restricts the cutting process to be uneven or cut out.
- Versatility: An air compressor, which enables you to tune the air pressure to the thickness and type of material you’re cutting, is necessary. Such versatility allows you to achieve perfect cutting for any application.
- Efficiency: The function of a compressor is to supply a constant stream of compressed air so you can work flawlessly without any breaks. This helps productivity and effectiveness when big or quick tasks are involved.
Understand the Working Air Compressor for Plasma Cutter:
This section throws light on the working of the air compressor for plasma cutter:
- Air Intake: The air compressor draws the surrounding air through its inlet valve.
- Compression: Now, the air is driven into the chamber at high pressure by means of a piston or a rotary screw.
- Storage: The air is compressed and stored either in a tank or reservoir and the plasma cutter is supplied by it whenever the need of the job arises.
- Regulation: A pressure regulator is a device that sets the airflow and permits the adjustment of output pressure to that of the plasma cutter.
- Delivery: The compressed air goes through the hoses to the torch that is turned into a plasma arc for cutting by being heated.
Part 2: How to Choose a Suitable Air Compressor for Plasma Cutter?
The right choice for air compressor for plasma cutter plays an important part in the work of the plasma cutter. By considering these factors, you can make the right choice:
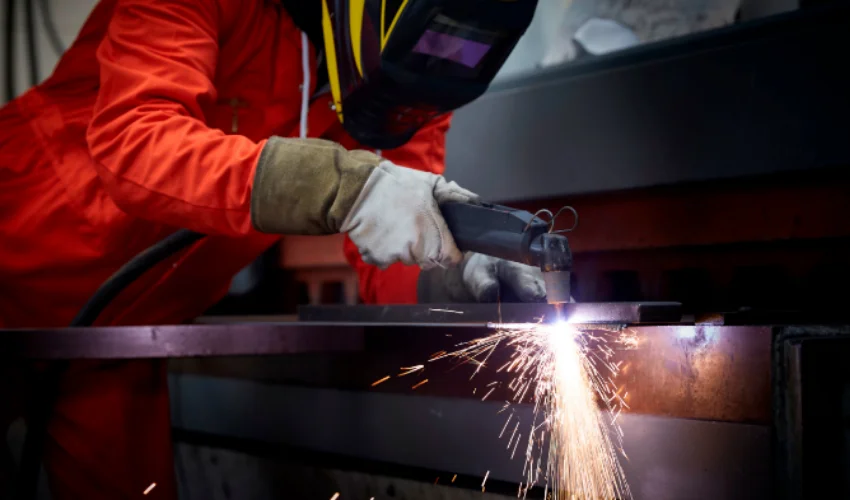
What size air compressor is needed for the plasma cutter?
The tank capacity represented by the compressor size in gallon. The amount of gas you have to provide depends on your plasma cutter’s need and the duration of the cutting job. The larger tank capacity means that the work can be done uninterrupted because there is no need for compressor refill.
For the light to the moderate cutting jobs, you will need 20 to 30 gallon tank. Nevertheless, the industrial cutting requires at least a 60-gallon tank or more for constant application of cutting sessions.
PSI (lb/in2)
PSI shows the compressor’s air pressure. Most plasma cutter types have a certain minimum PSI to function properly. Usually about 60 to 100 PSI. You have to buy a compressor capable of continuously giving you the needed PSI.
Check whether the maximum PSI of the compressor will meet or exceed the minimum PSI requirement by the plasma cutter. Also, shop for compressors with pressure settings that can be adjusted to manage cutting tasks and materials.
CFM (ft3/min)
CFM means the air volume delivered by the compressor in one minute. Plasma cutters may have different CFM requirements for size and duty rating. Insufficient CFM may lead to reduced power to cut and poor arc stability.
Establish the CFM needs of the plasma cutter by checking through the specifications or consulting the manufacturer’s guidelines. Select a compressor with a CFM rating that satisfies or exceeds the plasma cutting device’s requirements for smooth and effective operation.
Motor:
The air compressor’s motor plays a major role in its performance and durability. Seek out compressors with powerful engines of high quality to satisfy the power requirements of your plasma cutter.
Remember the power (HP) and motor efficiency when choosing an air compressor. These motors provide a larger air volume and higher pressure, which is good for cutting heavy-duty applications. Moreover, motors with thermal overload protection should be considered, as they shield from overheating and extend the compressor’s life.
Voltages:
Be mindful of the voltage requirements of your air compressor to match your power supply. Most air compressors run on the standard household voltages including, but not limited to, 120V or 240V.
Discover what the power capacity available in your workshop or workplace is, and purchase an air compressor rated for the power supply. The air compressor should never be used at an incorrect voltage, otherwise it might result in an electrical problem or equipment breakdown.
Noise:
Study carefully the air compressor’s sound level, especially in residential or noise-sensitive areas. Some compressors can make a lot of noise that can be disruptive and hence violate noise regulations.
Search for a noise reduction air compressor that comes with insulated enclosures and/or low-noise motors. In addition, pay attention to the place of the compressor and whether soundproofing materials will be necessary to reduce noise pollution.
Finally, consideration of all the needs such as tank capacity, PSI, CFM, motor quality, voltage compatibility and noise level is most important. Besides, you could get the best performance and efficiency in your cutting operations if you choose an air compressor that runs according to the requirements of your plasma cutter and your workplace.
Part 3: Best Air Compressor for Plasma Cutter
Summarizing how to pick the right air compressor for plasma cutter:
- Choose the air compressor with a sufficient tank size and PSI output.
- Make certain that the power of your compressor’s motor complies with your cutting needs.
- Do not forget to verify the voltage of your power adapter to ensure that it is compatible.
- Think about noise levels and look for quieter models if needed.
- Durability should be the first criterion that you look into.
Get insights on the best in class air compressor for plasma cutter down below:
VEVOR 80 Gallon Air Compressor
The VEVOR 80 Gallon Air Compressor was created for heavy-duty manufacturing processes, construction sites, and automobile mechanics. Thanks to a 6.5HP oil-free motor and dual-stage compression system, experience fast inflation and get 15.5 SCFM@90 PSI in as little as 6 minutes. The 80-gallon ultra-large capacity provides stability in air supply and prevents production accidents. Working under the low 86dB noise level it stops from interruptions. We use a 4mm high-strength steel plate to build it, which is durable and secure. It is perfect for pneumatic tools like drill guns and impact wrenches and is suitable for versatile industrial needs. Maximize your productivity using a stable air supply from VEVOR.
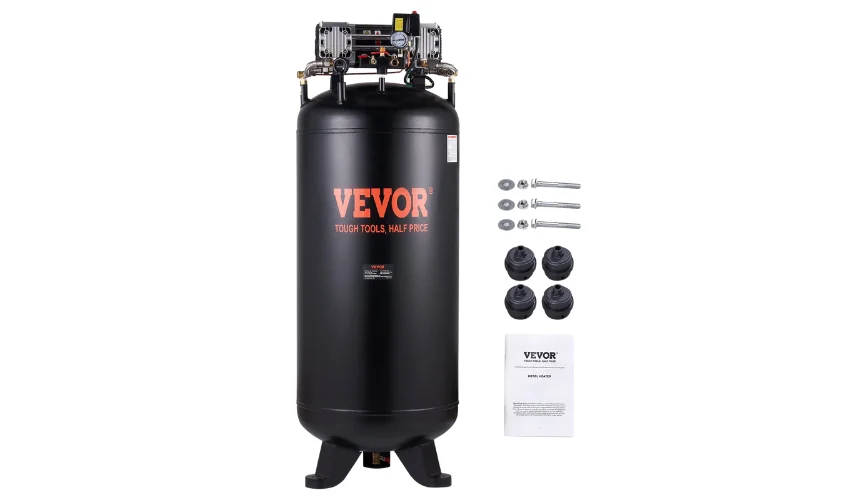
VEVOR 6.3 Gallon Air Compressor
Update your pneumatic toolkit with the VEVOR 6.3-gallon Air Compressor. The 6.3-gallon reservoir and 1450W oil-free motor provide an airflow output of 3.35 CFM@ 90PSI for jobs like tire inflation and spray painting. Its double-tube cylinder intake design takes advantage of rapid and easy inflation. Even though it is a powerful device, it works in an unobtrusive manner because of the dual silencers, at 70 dB. Designed and built with 3 layers of durability, it is protected against rust and wear and has safety features like automatic overheating protection. In the case of auto repair or woodworking, this compressor guarantees dependability and a relaxed mind in your projects.
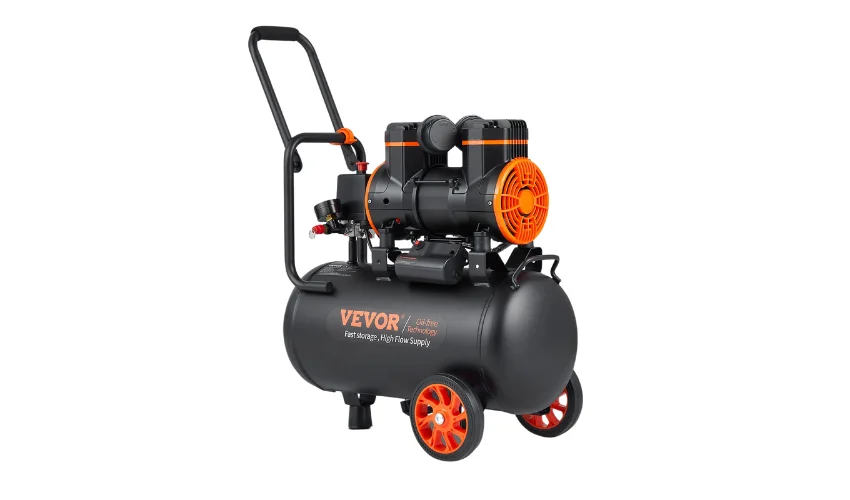
Part 4: How to Use an Air Compressor for Plasma Cutter?
Through the air compressor used in plasma cutting, you can reduce complications and chances of cutting tools failing. The key usage steps are:
Prepare Your Workspace:
Please check that your working place is ventilated and that there is no possibility of a fire appearing from combustibles. When selecting the place for your plasma cutter and air compressor, take into account the areas where you can operate without the requirement for extra space and electricity.
Check Air Compressor:
Ensure the power source is connected to the ground right and check for leaks if any. Adjust the pressure to suit your needs using the settings recommended by the plasma cutter manufacturer.
Connect Air Hose:
Fit an air hose from your compressor onto the cutter. All fastener points need to be attached, and the air does not come out.
Power Up:
While the air compressor is on too, initiate plasma cutting process. Just get the compressor to run until it reaches its desired button.
Set Cutting Parameters:
Spell out the parameters you need for plasma cutting, e.g. amperage and gas flow rate, to cut your desired material type and thickness.
Start Cutting:
Since everything is examined and re-checked, fire the plasma by pressing the shutter of the cutting torch, that is safe now. Ensure that you have an evenly rushing flame by making sure that there is always an equal distance between the glass and the cutting edge.
Monitor Air Pressure:
Make sure the air pressure gauge of your plasma cutter does not exceed the required range otherwise, it will not function properly. Adjust the compressor settings to fit the flow rate of air.
Finish and Shutdown:
When the cutting is completed, lighten the trigger of plasma cutter and cut off the air compressor. Disconnect the air hose and then place your equipment correctly.
Many types of plasma cutters come with built-in air compressors. They prevent you from buying another air compressor. The latter, however, offers some constraints in the way of high operational costs and lack of mobility, making it less portable than conventional air compressors.
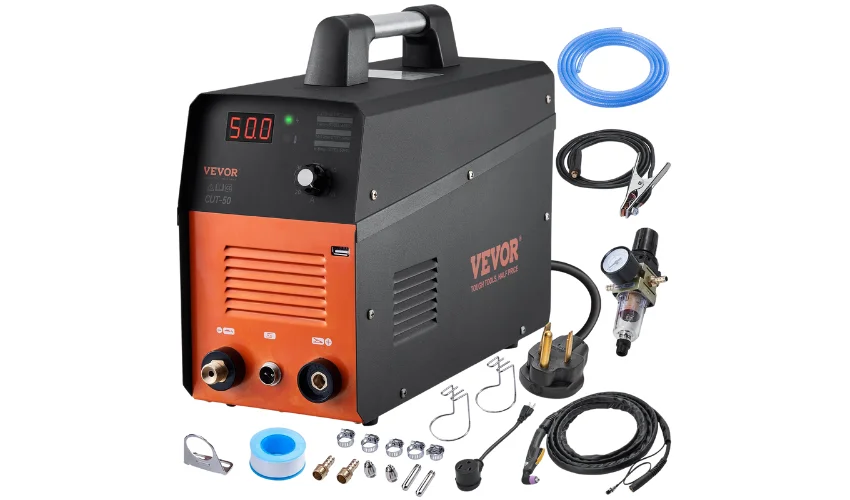
Conclusion
The selection of the right sized air compressor is paramount to productive and precise cutting operations. Learn how pressure, cooling, and protection help you optimize your performance while cutting. Forget to choose an air compressor fitting with your plasma cutter. Never let bad equipment spoil your performance. It is about time to transform your appearance and show your best reflective features. Investigate VEVOR’s air compressors that are specifically manufactured for plasma cutting needs. Now, you have the option to have an easier and better slice the next day.
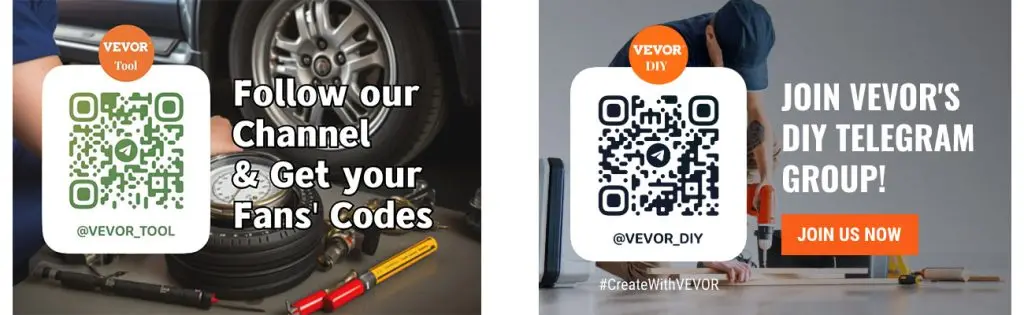