When delving into the world of metal fabrication and precision cutting, understanding the tools at your disposal is crucial. Among these tools, the plasma cutter stands out for its ability to slice through various metals with precision. But have you ever wondered how hot is a plasma cutter arc? In this exploration, we’ll uncover how hot is a plasma cutter and shed light on the factors affecting it. Moreover, we’ll present a comprehensive set of tips to help you modify the temperature of your cutter. Also included in our blog are some key safety considerations. Stay tuned and keep reading!
Table of contents
How Hot Can a Plasma Cutter Get?
So what is the temperature of a plasma cutter when it’s working?
A plasma cutter generates extremely high temperatures to effectively cut through various materials. The temperature of the plasma arc produced by a plasma cutter can exceed 20,000 °C (36,032 ℉). To put this in perspective, let’s see some figures. The oxyacetylene flame is usually 3,000 °C (5,432 ℉), the surface of the sun averages around 5,500 °C (9,932 ℉), and the temperature of lightning can reach 30,000 °C (54,032 ℉). As we can see, the temperature of the plasma arc is on the same order of magnitude as that of lightning.
How can plasma cutting be this hot? For plasma cutting, the initial step involves passing compressed air or gas through the torch nozzle. This gas is then subjected to an electric arc, a high-voltage electrical discharge. The energy from the electric arc ionizes the gas, stripping electrons from the atoms and creating a state of matter known as plasma and at the same time producing intense heat, raising the temperature of the plasma. This is how the extreme heat comes about in a plasma cutter.
However, it should be noted that not all plasma cutters generate the same amount of heat. In fact, there is a web of factors determining how hot does a plasma cutter get. In the upcoming part, we’ll deal with these factors and elucidate how they affect the cutting temperature.
What Affects the Temperature of a Plasma Cutter?
Multiple factors work together to determine what temperature does a plasma cutter cut at. Now let’s see a breakdown of the key factors contributing to the high temperature of a plasma cutter.
Gas Selection
The choice of plasma gas significantly impacts the cutter’s temperature. Different gases, such as nitrogen or oxygen, possess varying thermal conductivities and ionization potentials, affecting the arc’s temperature.
Air Pressure
The pressure of the compressed air or gas passing through the plasma cutter is another crucial determinant of temperature. Higher air pressure typically contributes to a more intense and hotter plasma arc.
Material Thickness
The thickness of the material being cut is directly related to the required temperature for effective cutting. Thicker materials demand a hotter plasma arc to achieve successful melting and penetration.
Quality of a Plasma Cutter
The construction, components, and overall build quality of a plasma cutter significantly influence its performance, including temperature control. The construction, components, and overall build quality of a plasma cutter significantly influence its performance, including temperature control. So we advise you to use high-quality plasma cutters from renowned brands like VEVOR. They are typically equipped with efficient heat management dissipation systems, allowing for consistent temperatures during operations. For example, the VEVOR Pilot Arc Plasma Cutter and VEVOR Air Cutter with Plasma Torch feature a unique air channel design and professional cooling fans, ensuring optimal performance during long-time cutting tasks.
Other Factors
Aside from the ones listed above, some other factors also play a role in determining how hot does a plasma cutter burn, including cutting speed, power source stability, gas flow rate, and more which should also be taken into consideration when making a plasma cutting.
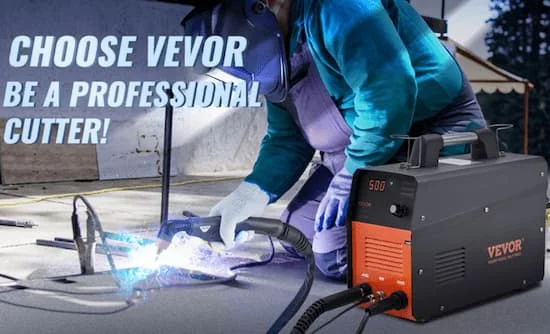
How to Modify the Temperature of a Plasma Cutter?
Modifying the temperature of a plasma cutter involves adjusting several key parameters to optimize its performance for cutting different materials and thicknesses. In the next part, we’ll list some essential tips to help you modify the temperature of your cutter.
Adjusting Current (Amperage)
In a plasma cutter, the temperature of the plasma is directly proportional to the current intensity passing through the plasma. The higher the current, the more intense the heat of the plasma arc. Therefore, controlling the current is a crucial factor in regulating the temperature of the plasma cutter.
Gas Flow Rate and Composition
The flow rate regulates the amount of gas available for ionization, affecting the plasma arc’s intensity and temperature. A higher flow rate increases gas velocity, leading to better heat transfer away from the cutting zone and lower cutting temperatures. On the other hand, the gas composition influences thermal conductivity and ionization potential, directly influencing the temperature.
Nozzle Size and Design
The nozzle constriction affects the flow dynamics of the plasma arc, influencing its temperature. For example, smaller nozzles can result in higher temperatures due to increased gas velocity and concentration. By changing the nozzle size and design, you can fine-tune the temperature to your needs.
Torch Angle and Standoff Distance
Torch angle and standoff distance influence the concentration of plasma and hence the temperature. A perpendicular angle creates a focused plasma jet, resulting in high cutting temperatures. On the other hand, a nearer standoff distance concentrates the plasma’s energy, raising the cutting temperature.
Material-Specific Considerations
The material of the workpiece plays a significant role in determining the cutting temperature. For example, harder materials with higher melting points may require more heat, requiring higher temperatures for effective cutting.
Power Source Settings
Power source settings in a plasma cutter, such as voltage and amperage, directly impact the temperature during the cutting process. Higher voltage and amperage settings generally result in a more intense and hotter plasma arc, and vice versa.
Operator Techniques
The operator techniques can also affect the cutting temperature. Factors such as travel speed, cutting angle, and consistency in motion significantly influence the heat input and, consequently, the temperature of the cut. For example, a slower travel speed can increase heat exposure to the material, potentially elevating the temperature.
Environmental Conditions
Lastly, environmental conditions can impact the temperature of a plasma cutter in various ways. For example, inadequate ventilation can hinder the dissipation of heat, resulting in a higher temperature and overheating hazards.
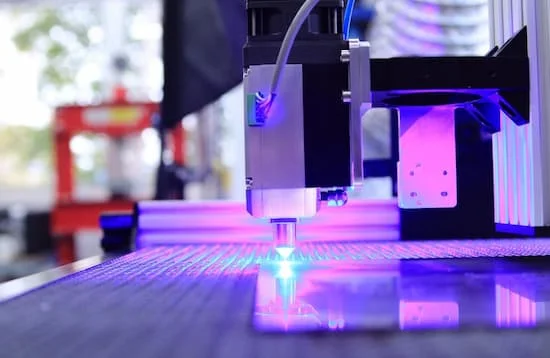
Plasma Cutter Safety Considerations
Safety is always paramount, especially when handling something that can produce extreme temperatures. Below are some primary safety considerations to help you steer clear of safety hazards.
Personal Protective Equipment: Always utilize suitable personal protective equipment (PPE), such as a welding helmet with the correct shade, flame-resistant attire, gloves, and protective eyewear.
Ventilation: Ensure proper ventilation in the workspace to remove fumes and gases generated during cutting. Use exhaust systems or work in well-ventilated areas.
Fire Safety: Keep a fire extinguisher nearby and be aware of the flammability of materials being cut. Remove flammable materials from the work area.
Eye Protection: Use appropriate eye protection to shield against intense light and UV radiation generated during plasma cutting.
Modifying Plasma Cutter Temperature for Different Applications
Plasma cutters are versatile tools, and by adjusting how hot is a plasma cutter flame in various ways, they can be tailored to suit a diverse range of applications. Below are some scenarios and how you can modify the temperatures for each of them.
Thin Sheet Metal Cutting: When cutting thin sheet metals, lower temperatures are used. This is because lower temperatures prevent material distortion and warping, while still being hot enough to sever the metal sheets neatly. Typically, lower cutting temperatures are achieved by reducing the voltage and amperage of the cutter.
Fine Detail Cutting: In the case of fine detail cutting, using a smaller nozzle for fine detail work helps concentrate the plasma arc, creating a higher local temperature. This allows for intricate and precise cuts without excessive heat input.
Different Materials: Working with various materials, such as aluminum, stainless steel, or mild steel, requires adjusting the gas flow rate to create varying cutting temperatures. This is essential to account for differences in the thermal conductivity and material reactions.
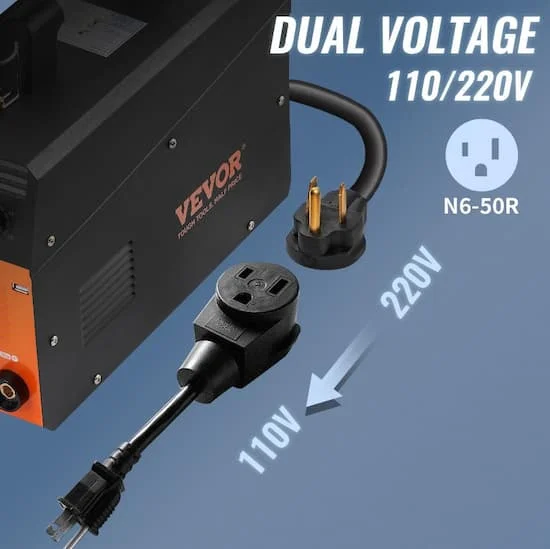
FAQ
Is a Plasma Cutter Hotter than the Sun?
Yes, a plasma cutter can achieve temperatures hotter than the surface of the sun. While the sun’s surface averages about 5,500 degrees Celsius (9,932 Degrees Fahrenheit), a plasma cutter can reach temperatures exceeding 20,000 degrees Celsius (36,032 Degrees Fahrenheit). However, despite exceeding the surface of the sun in hotness, the temperature of a plasma cutter can’t even remotely rival that of the solar core, which boasts a staggering 15 million degrees Celsius (about 27 million degrees Fahrenheit).
Do Plasma Cutters Overheat?
Yes. Plasma cutters, like any machinery, can overheat if used improperly or subjected to excessive demands. Overheating may occur due to factors such as prolonged use beyond the recommended duty cycle, inadequate cooling, or operating in high-temperature environments. However, quality plasma cutters (such as VEVOR’s lineup) often incorporate built-in cooling systems to dissipate heat and prevent overheating, making sure the cutter works in optimal states.
Can a Plasma Cutter Start a Fire?
Yes, a plasma cutter has the potential to start a fire if not used with caution. The intense heat, sparks, and molten metal fragments generated during the cutting process can ignite flammable materials in the proximity of the work area. This is why safety measures are paramount during plasma-cutting operations.
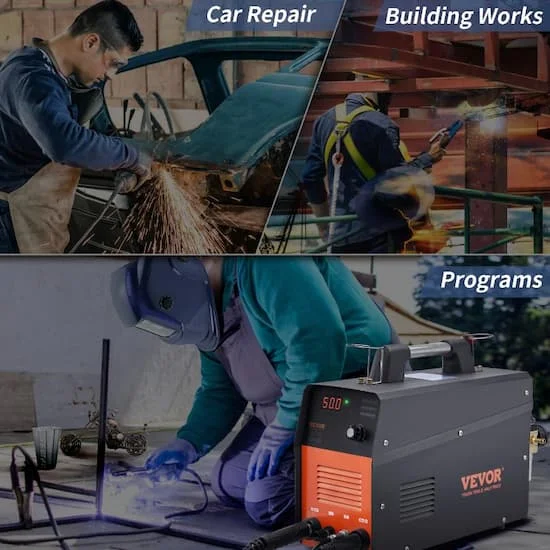
Conclusion
From our discussion above, it is clear that the precise control of cutting temperature ensures efficiency, accuracy, and safety in metal fabrication. It is therefore crucial to gain a thorough understanding of the temperature of plasma cutters and the myriad of factors affecting it. By learning about the major factors affecting how hot is a plasma cutter plus the ways to modify it, you can leverage your tools more skillfully and ace your metalworking projects.
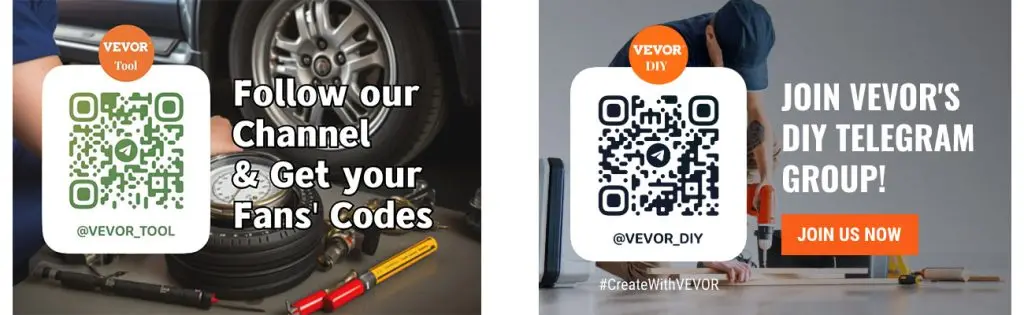