The accuracy and efficiency of Plasma cutters are undeniable. But they sometimes encounter quality, pressure, or electrical issues that hinder your metalworking. And then it comes to you that the best option is to purchase a plasma cutter troubleshooting guide to fix the issue on your own before seeking professional services.
Therefore, we will talk about why the plasma cutter troubleshooting should be done safely and what tools you need to have at hand in today’s tutorial. In other than that, you will be trained on three methods of maintaining your plasma cutter to make sure that there is no downtime when working on another creative project.
Table of contents
Why Plasma Cutter Troubleshooting Matters?
You can cut down extra expenses or save your time using this Plasma cutter troubleshooting guide. But first, you need to understand the importance of safety elements with the cutter and how it actually works:
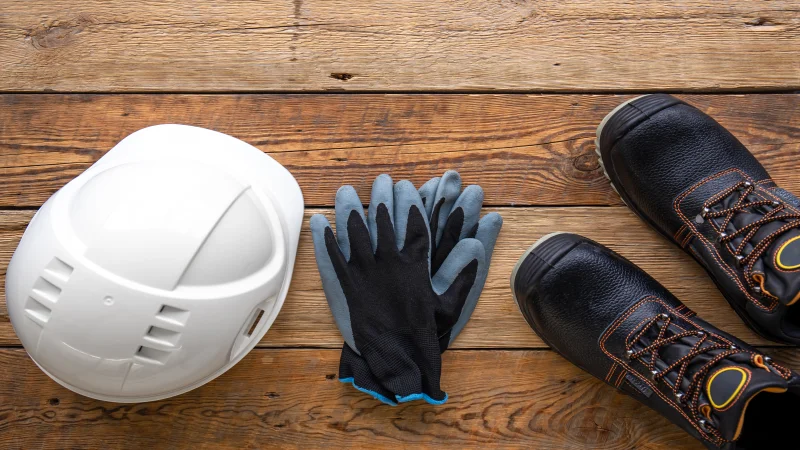
Deepen Safety Awareness
Plasma cutters usually emit high heat due to the metal-cutting process and intense UV radiation. For this reason, you need to make a checklist of safety gear to prevent any injuries and accidents while troubleshooting the machine. These include:
- Use safety goggles to ensure eye safety from debris, UV rays, and sparking.
- Make sure to wear flame or fire resistant clothes to protect yourself from accidents or injuries.
- Use oil-free leather gloves to shield your hands from excessive heat produced while cutting heavy metals.
- You must also have with you durable steel-toed boats with leather soles to protect your feet from the heaving objects falling and electric shocks.
- Use earplugs to shield your ears from loud noise and a respirator with proper filters so you don’t inhale harmful fumes.
- Wear a welding mask or helmet with a shade number 11 protective filter.
Before plasma cutter troubleshooting, turn it off and remove the power cable from the power source. Then, thoroughly read the cutter’s user manual to understand any details indicating the problem at hand.
If you fail to understand the details, access a plasma cutter troubleshooting guide for easy step-by-step instructions.
Learn How Plasma Cutting Works
Before fixing your plasma cutter problems, you need to know how the machine operates:
It has some basic components that are essential for proper working. These are:
- Power supply for converting AC voltage to DC.
- Plasma torch for creating and controlling the plasma arc.
- Air compressor and plasma cutter.
- RHF console for water and gas plumbing.
Some plasma cutters also have a non-touch pilot arc, like VEVOR.
Furthermore, a few cutters come with different technologies like waterjet cutting, laser-guided, dual-gas for metal with high conductivity, precision piercing, and multi-pass cutting.
Necessary Troubleshooting Tools for Plasma Cutting
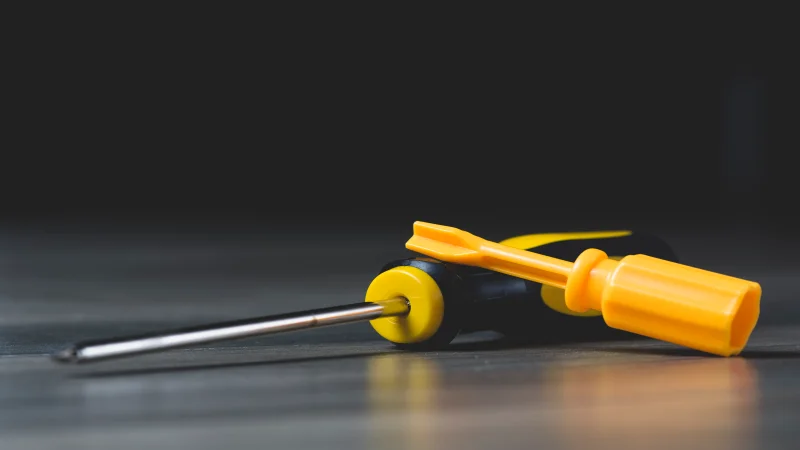
While following the plasma cutter troubleshooting guide, you’ll need some necessary tools to diagnose and resolve the issues with the machine. Let’s discuss them below:
1. Screwdriver
A screwdriver comes in handy to open certain components of your plasma cutter during the repair process. So it is best to always keep it nearby. Do remember to hold it firmly when removing the screws of each part of the machine.
2. Multimeter
By using the multimeter you can observe the electric parameters including the voltage, resistance, and even current.
Be sure to calibrate it in the correct range for your particular parameter of measurement, and this will enable you to determine which components are faulty in the cutter.
3. Air Pressure Gauge:
As an essential part of your welding cart, you should keep an air pressure gauge that can check the pressure in either the compressor or air tank attached to the plasma cutter. This allows it to comply with the cutting process. If one of them goes bad, you will lack the correct pressure and flow to cut the metal.
4. Zero-Contact IR (Infrared) Thermometer
Zero contact IR (infrared) thermometer fully capable to record the operational temperature of your plasma cutter.
For the thermometer to function, hold it slightly above the surface and then squeeze on the trigger that activates its sensor for readings displayed on a screen.
5. Consumables Kit
You’ll also need a consumable kit containing shields, electrodes, and nozzles. It will keep you going while quickly replacing these parts on your plasma cutter.
Try to store the kit in a clean and dry place like your 2-tier welding cart, and use the proper tools to install the consumables.
Common Issues Addressed in Plasma Cutter Troubleshooting Guides
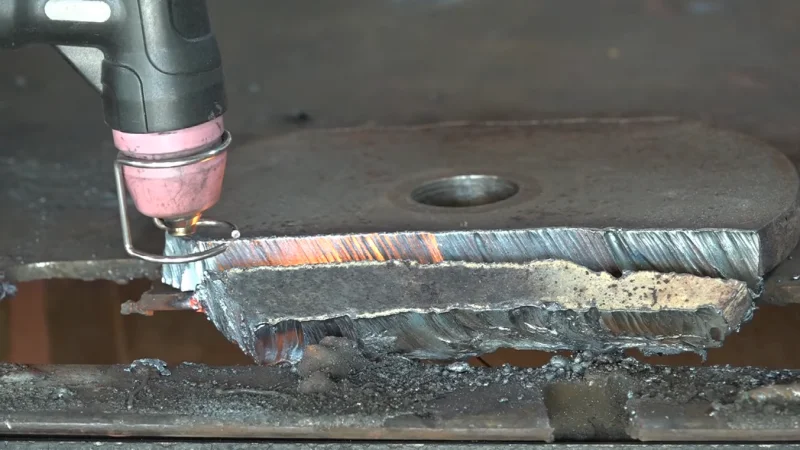
Below, we’ll point out a few common issues in this plasma cutter troubleshooting guide that can affect its performance quality.
1. Poor Cutting Quality
The plasma cutter is the most productive metal cutting machine due to its low operational cost and correct-fast speed. However, it has certain interdependent variables that often lead to poor cut angles, dross, and surface roughness if you set them incorrectly.
These include:
- Torch alignment and type.
- Gas type, pressure, and flow.
- Thickness of the material.
- Speed of cutting
- Height of cutting – Arc voltage (THC)
The best practice here is to inspect the torch alignment and check the condition of the consumables, such as the nozzle, electrode, and shield cap, before cutting metal. Set air pressure and flow according to the thickness and type of metal you are trying to cut.
To avoid dross and get a polished surface finish, configure the cutting speed and torch height of the machine according to the cutting material.
2. Weak Or Inconsistent Arc
If the plasma cutter not arcing, this happens when there is poor contact between the ground wiring and the workpiece. Sometimes, too high or low air pressure and burnt-out touch nozzle or electrodes also result in this frustrating issue.
To fix this, check the wire attached to the ground clamp and see if it is securely connected to it. Also, use a specialized grounding tool to identify any insulation that can adversely impact the connection between the surface of the workpiece and the ground wire.
Moreover, before cutting metals with the plasma machine, inspect the output of the air compressor and use the regulator to make necessary adjustments for optimal air pressure.
Also, confirm that the torch nozzle is installed firmly and the fitting around the electrode holder is not rough to avoid the burnt-out issue.
3. Air Supply Problems
Another major problem that most plasma air-cutting machines face is insufficient airflow rate or pressure. Since each manufacturer, like VEVOR, has its own pressure requirements, you have to set the compressor accordingly to avoid the plasma cutter wont arc and other issues.
To do this, check the plasma cutter manual and use the pressure regulator on the side of the machine to adjust the settings.
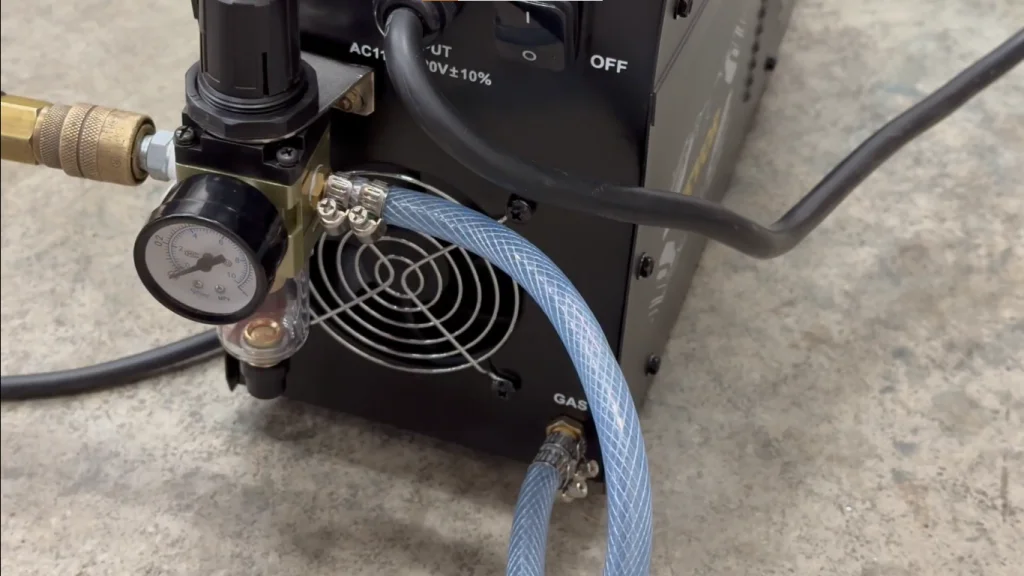
If your plasma cutter has an insufficient flow rate at the air inlet even when you correctly configure the pressure, this could be due to the following reasons:
- Contaminated air filters.
- Dust and debris stuck in the air line.
- Incorrect air hose diameter.
In such a scenario, it’s best to remove the filter from your plasma cutter and replace it so that it can efficiently purify the air for the machine.
To clean the air line, disconnect it at the joints on your plasma cutter, insert a cleaning pad into it using a steel rod to remove the debris, and reconnect it. Now, run the compressed air through the air line so that the dust comes out of the other end.
In case, this doesn’t help with the issues and your plasma cutter just blowing air, replace the air hose with the one that meets the standard requirements for your machine.
4. Electrical Issues
Sometimes, the main power supply unit does not provide adequate power to your plasma machine. Due to this, you experience inconsistent performance and often end up thinking why does my plasma cutter keep stopping?
The quick solution here is to ensure the power supply does not fluctuate and meets the specifications of your plasma cutter.
Besides this, inspect the earth clamp and use the infrared thermometer to check if its temperature is high. If so, simply replace the clamp with a new one.
The Proper Way to Maintain Your Plasma Cutter
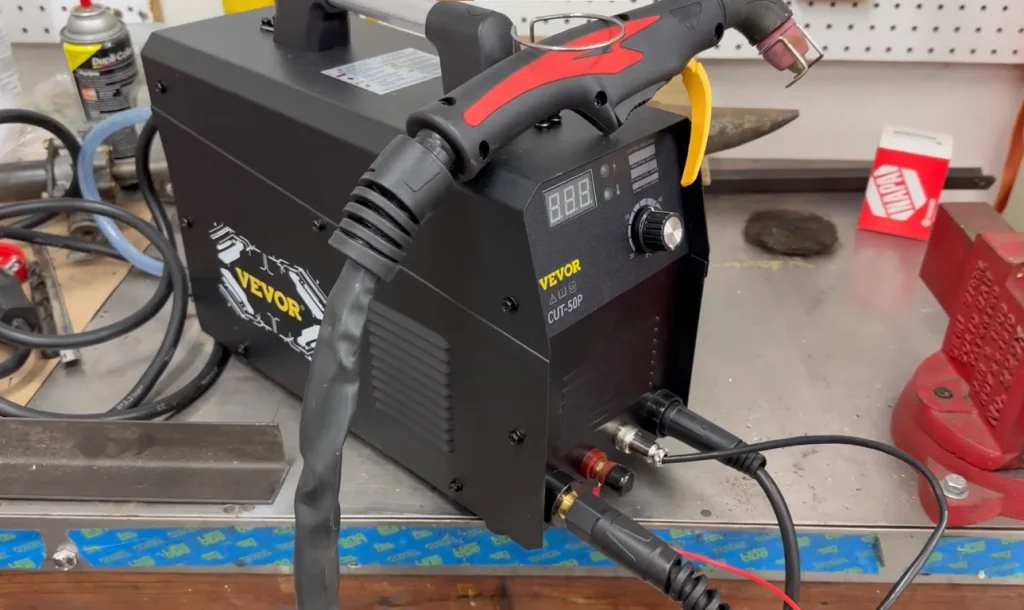
Proper maintenance of your plasma cutter can make it last a while.
That’s the reason we’ve listed below 3 steps to maintain your machine in this plasma cutter troubleshooting guide.
1.Regular Cleaning And Monitoring
The first thing you need to do is regularly clean your plasma cutter. The most important bit for this purpose is cleaning the torch with a cotton swab and an electrical contact cleaner and blowing out any accumulated metal dust from the lead fittings.
Also, use a can of compressed air to remove dust or debris from the power supply of your plasma cutter.
Besides cleaning the plasma machine, you also need to regularly inspect the following parts:
- Visible damage on the torch threads.
- Air filters for any contamination.
- Coolant level in the machine.
- Gas quality in the cutter by holding a clean paper towel under the torch and purging the air.
- Inspect all the hoses and lead for any damage or dust/debris.
- Check the coolant system for leaks (at least once per month).
Always keep the necessary tools and equipment near you in a welding cart to clean and monitor your plasma cutter in a timely manner.
2. Lubricating The Moving Part
It’s also a good practice to use a dry lubricant (graphite powder) on the cutter’s gears and bearings. But don’t use it on the rail section as it will attract more dust (and other contaminants) and damage the machine.
3. Seeking Professional Help When Needed
If you find that the issue is above your expertise level and you cannot fix it with any plasma cutter troubleshooting guide, seek professional help on time. Otherwise, you’ll damage your machine beyond repair and end up spending thousands on fixing or replacing it with a new one.
FAQs
What Is A Common Issue When Plasma Cutting?
Poor cutting quality is the most common issue with plasma cutting. This usually arises when you are not handling the torch correctly or the consumables are defective. To prevent this, do not press the torch against the workpiece and replace its nozzle and shield with new ones from time to time.
Should The Plasma Cutter Tip Touch The Metal?
If the plasma cutter tip touches the metal, they’ll fuse together and cause the cutter to stop working. To avoid this, use “Drag cups” or “‘Drag shields” to maintain a safe distance and help you follow a pattern in the metal or draw a straight line easily.
How Often Do You Change The Tip On A Plasma Cutter?
If the hole in the plasma cutter tip gets larger, resulting in a thicker arc and a wider cut, it’s time to change it. Generally, the tip lasts 1-3 hours at about 120 A of regular cutting.
Why Does My Plasma Cutter Keep Losing Arc?
Your plasma cutter keeps losing arc when you incorrectly set the air pressure or the torch nozzle and electrode are burnt out. To fix this, use the pressure regulator to configure the gas output of the compressor on your plasma machine. In case this fails, change the torch nozzle and electrode in the cutter.
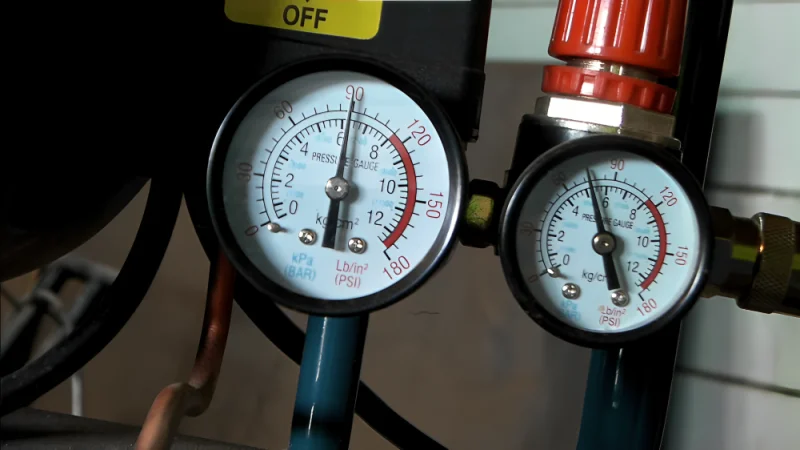
What Is The Best Setting For A Plasma Cutter?
Multiple factors play a key role in helping you decide the best setting for your plasma cutter. These factors includes metal thickness, metal type, melting point, etc. The setting also depends on the plasma cutter you are using. In general employ high temp for thicker metals and lower temp for thinner metals.
What Psi Should A Plasma Cutter Be Set At?
For a small handheld plasma cutter that works at 20-30 amperage, you will require only 80 psi. Meanwhile, for larger, automated machines (running at 130 to 800 amps), you’ll need around 115 or above psi.
Conclusion
In this plasma cutter troubleshooting guide, we’ve discussed its significance, along with safety measures and the working of the machine. We’ve also explored some necessary tools that you’ll need during the diagnosis and repair process and addressed some common issues and their solutions.
Remember, a reliable cutter and DIY tools can transform your metalworking project from good to great. That’s why VEVOR offers a range of high-quality, durable, and affordable plasma-cutting machines.
So, why wait? Go on and explore the VEVOR plasma cutters and other tools for your workshop now!
